Airslide Fabrics
Dusol Technologies air slide Fabrics are used to convey bulk material either as granulate or as free flowing powder.
Areas of usage
- Cement industry
- Aluminium, chalk and gypsum industries Coal-fired power stations
- Chemical industry
- Pharmaceutical industry
- Powder coating industry
Our air slide fabrics are produced from a range of top quality materials and yarns. Our customer's benefit from a choice of materials which enable them to specify the thickness, air permeability, mechanical strength and temperature performance needed.
The suitability of a fabric for a specific application de- pends on factors such as:
- Type of bulk material, particle size, operating tempera ture and moisture content of the material to be transported or discharged
- Environmental factors such as ambient temperature and humidity
Type of equipment
The Benefits & Advantages of PTFE Treatment
XL 596 finishes for the conveying of cement through Fluidized Bed System
The major advancements in the cement and other industrial standards have seen a sea of change.This change has crept in form the technological advancements from the engineering slide in particular. The material handling in sense through the pneumatic systems in practice with the industry has brought a new window to many people. One such area application comes the conveying of the material through the fluidized bed system wherein the material to be conveyed is made airborne & conveyed through the gravity through slight angles of inclinations. This was very well than said when fewer amounts of materials are involved in the process but when the system involves higher volume and quantities of materials there are many more complexities that are faced few of which are:
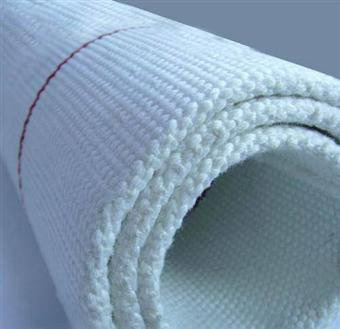
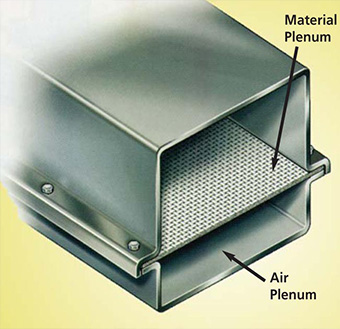
- Higher volumes meaning greater amount of the base pressure is applied to elevate the Materials Higher pressure meaning greater stress on the fabric
- Let us not forget that the air pressure which is transferred & forms a “pericardial layer of air between the material & the Cloth” with the inclination in hand forms the eddy ripples in the material above this material which is under transit further creates an momentum which is applied to the base fabric to make the minute particles to flow back under the fabric & cling the second layer ofthe air slide fabric.
- During the time of higher moisture from any pulverize sources or other media there is on added problem of coagulation of fine particles in the pores of the air slide fabric.
- At times of higher pressure exerted from the blowers the CDV (Cloth Drag Velocity) increase which in turn forms greater wear & tear of the above material.
- All said is well when the above is only run with the lower or ambient temperatures & ordinary gases.
- At elevated temperature the chemical attacks on the base fabric is calculated to be hire by 3 timesand is said to even corrode the toughest of the materials including stainless steel or other.
- As being basically a woven media the fabric when it’s taken into constant to and fro elongation loses its basics property and becomes completely in elastics in nature.
- All the above properties of solved by Dusol Technologies through a special treatment done names XL 596 finish. The above is basically a Poly-Tetra Fluro Ethylene pigment chemical which is applied to the above fabric through dip method.This treatment is given taking in mind, the above problems faced.
Thermal Characteristics and Chemical Resistance
Technical characteristics of dusol technologies
Dusol technologies fabrics are made of high strength polyester fibers. These materials are highly resistant to chemicals. With the use of stream. Alkaline or acid substance their durability is reduced. The higher the temperature of concentration of chemicals substances, the faster the durability of the fibers dissipates.
The beneficiaries of the above treatment are as follow:
- A Shield against the continuous abrasions in the fabric.
- A moisture repellent finish which does not allow the moisture to effect neither the base fabric nor allow any chemical attacks on the above fabric.
- The above also does not allow the coagulation of the minute pores of the fabric & hamper its performance.
- The CDV is further reduced by the slippery surface finish of above chemical.
- Due to the dip finish the treated chemical tries to couple the fibers to an appreciable level & increase the life of the base fabric
- In an overall scenario the above finish enhances the life of base fabric.